Deakin University metallurgist Dr Nima Haghdadi is pursuing cutting-edge research in the field of 3D metal printing, thanks to a prestigious Victoria Fellowship.
High entropy alloys have huge commercial potential for products ranging from electrical wiring, to aircraft parts, to mining components. Dr Nima Haghdadi, an Alfred Deakin Postdoctoral Research Fellow, is hoping to help keep Australia at the forefront of research in this lucrative field.
He will undertake a research mission to the Max-Planck-Institut für Eisenforschung in Germany in December, through a coveted Veski Victoria Fellowship.
Dr Haghdadi, who is based within Deakin’s Institute for Frontier Materials, will spend two months at the Max-Planck Institute, focussing on improving thermal dynamic 3D printing processes for high entropy alloys. These are a revolutionary type of metal alloy that contain an assortment of different elements and properties.
One of the main challenges faced in high entropy alloy production has been that each element within an alloy has a different melting temperature. This means that trying to make an alloy through traditional melting (casting) or even heating an entire alloy at once can lead to interference with the metal properties once the alloy solidifies, potentially affecting its overall strength.
“Imagine that you want to melt aluminium with a melting point of 660⁰C and cobalt with a melting point of 1495⁰C,” Dr Haghdadi explained. “You want to melt the one element, but the other one may vaporise. It’s very, very difficult.”
Printing a net-shaped high entropy alloy with 3D printers, however, would eliminate this problem. The metals are turned into powder by atomizing processes. These can then be sculpted into a new object without its melting point being reached to favour that of another metal.
“You still need some high temperature during the printing process to ensure a strong bond, and some cycles of heating and cooling will be applied, but the problems faced in the traditional casting process aren’t there,” explained Dr Haghdadi.
[testimonial_text]This process would also allow for other forms of metal to be more easily recycled. Broken parts that would otherwise have no other use could be melted down, turned into powders and finally 3D printed into an alloy, which could then be printed into a new object that harnesses the superior properties of each material. It also reduces waste, achieving cost and material savings.[/testimonial_text]
[testimonial_picture name=”Dr Nima Haghdadi” details=”Deakin University Institute for Frontier Materials”]
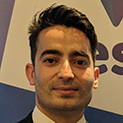
Making strong alloys can be beneficial to a wide range of industries including aerospace, automotive, energy and mining. As an example, for the mining sector, Deakin’s Institute for Frontier Materials is currently carrying out extensive research on development of new wear-resistant alloys.
“A lot of digging equipment is made from metals,” Dr Haghdadi explained. “Making them last longer would achieve huge cost savings for this sector and aligns with other research being done at Deakin through mineAlloy (the Deakin-based ARC Training Centre in Alloy Innovation for Mining Efficiency).”
“If some of these drill parts were to be made from high entropy alloys, which are displaying good wear-and-tear properties, then they could last significantly longer, creating an opportunity to save money along the way.”
The Max-Planck-Institut für Eisenforschung is a world leader in metals research, keen to share its wealth of knowledge with early career researchers. Dr Haghdadi is rightly proud of his Fellowship achievement.
“As researchers, we spend a lot of late nights working hard, and many times our experiments go wrong for no reason! Receiving a Fellowship like this makes you realise that it was all worth it. Somebody recognises the hard work you are doing. That’s a very good feeling,” he said.
Not only will Dr Haghdadi be able to continue his research surrounded by experts with new insights, but he will be exposed to other exciting opportunities and knowledge at the Institute.
“These are highly specialised areas of research,” he said. “This is something you can’t learn from a book or the Internet. I selected Max-Planck for my research in particular, as over there I will be working with world-leaders in several areas and have access to many world-class instruments. I will be able to learn a great deal in a relatively short period of time.”
He is excited about bringing the fruits of his overseas research back to projects in Australia.
Main photograph: Dr Nima Haghdadi with Professor Peter Hodgson, Vice-President Industry and Engagement, Innovation and Commercialisation.
Published by Deakin Research on 20 November 2018