Builders and architects are swooning. A small Australian start-up has achieved what they thought was impossible: the ability to create sharp bends in corrugated iron – a world-first that is set to transform the future of architecture.
It has taken some time, as many good ideas do, but after two generations of innovative Aussie engineers put their minds to it, a process and technology now exists that is likely to step-change the future of corrugated iron.
Backed by Deakin University and others, the Geelong start-up FormFlow has patented its innovative process and set up at Deakin’s ManuFutures to take its technology to the world. At its helm are two of Geelong’s most innovative engineers/metal formers: Dr Matthew Dingle and Dr Matthias Weiss.

Dingle was one of the brains behind Geelong’s great 21st century business success story, Carbon Revolution, which began in Geelong in 2006 with four young innovators. The one-piece, carbon fibre wheel manufacturer has attracted global giants as clients and brought hundreds of high-end jobs and many millions of dollars of investment to the region. Early indications are that FormFlow will follow suit.
The Japanese art form of paper folding, Origami, was the genesis for the innovation behind FormFlow. The folding of corrugated sheets of paper has long been practised by Origami experts. But Origami is an art. The engineers who saw its potential knew that to apply this to strong metals in manufacturing, they needed to understand the science behind it.
The breakthrough was made by two Australians, Jim and John Duncan, cousins, who, at the time were working at different universities in Canada. They discovered the geometric theorems governing the folding of curved surfaces and their work was published by the Royal Society in London in 1992.
The significance of their work was that these surfaces, folded developables, could now be designed in the modern computer-aided design (CAD) systems used by engineers for die design. Some years later, John Duncan became associated with sheet metal research at Deakin and was a mentor to both Matt Dingle and Matthias Weiss during their PhD studies.
Together, they produced the first scientifically-designed forming system to fold corrugated sheet and make the FormFlow bend.
Can FormFlow disrupt the construction industry?
The stand-out feature of FormFlow is its potential to apply revolutionary technology broadly. It opens a whole range of new possibilities for the structure of any building – offering new ways to form, assemble and manage building projects.
“I think we can disrupt the construction industry,” said Dingle. “Buildings are low-tech currently. Today, vehicle production is fully automated, with robotic production lines achieving incredibly tight tolerances, while keeping costs low. This minimises construction errors and waste, both of which contribute significantly to the cost in current building practices.
“Adopting similar principles for buildings is a hugely practical option for the construction industry. We believe we can help builders construct a new building with higher performance at a fraction of the price and our FormFlow technology is one of the key elements to achieving this.”
“FormFlow bends are structurally stiff and strong, airtight and they look fantastic,” added Weiss. “Because we can make a structure seamless, we eliminate the need for capping, and improve energy efficiency and fire resistance. We can achieve a range of angles. Our 90-degree angle is of huge interest to builders.”
Creating ideas at ManuFutures

The two entrepreneurs chose Deakin’s ManuFutures development facility in Waurn Ponds as their base, particularly for its “ideas” culture. Twelve innovative, high-tech start-ups are located on-campus, as well as some of the best materials and engineering experts and facilities in the world at Deakin.
The duo have the perfect track record for advancing FormFlow. Since joining Deakin in 2002 from Germany, Weiss has set up the world’s biggest and best-resourced roll forming research group (at Deakin’s Institute for Frontier Materials), which supports three post-doctoral researchers and six PhD researchers and is attracting accolades from sheet metal fabricators globally.
An entrepreneur’s tips for success
Matt Dingle is a serial entrepreneur and inventor. He worked at Ford Geelong’s Product Development Facility in the 1990s, and completed a PhD at Deakin before setting up three small companies, where he cut his teeth on start-ups. He then co-founded Carbon Revolution, where he remains a shareholder and his brother Jake continues as CEO.
“At Carbon Revolution, we were interested in how you commercialise an idea,” said Dingle. “FormFlow has been the same. Various patents for different ways to form inextensible sheets have existed for some time. The challenge was working out how to physically do it. For both companies, we had to think differently.”
Staying enthusiastic when money is tight and a product is still in development is one of the hardest challenges of setting up a business, according to Dingle.
“Also, Australian culture can be a bit insular,” he said. “Many people try to set up new businesses alone, but that often doesn’t work. You need to be confident – pig-headed – and you need a good team of people who are all different, so you can learn a bit from everybody.”
Corrugated iron itself is an astounding success story. Many Australians think of it as our own, but, in fact, it was developed in England in the 1830s, flourishing everywhere, particularly during the gold rushes, where its light weight, strength, corrosion-resistance and portability were ideal for mass migrations. It suited Australian conditions perfectly and has become part of our story. It was even showcased at the 2000 Sydney Olympic Games, in “Tin Symphony.”
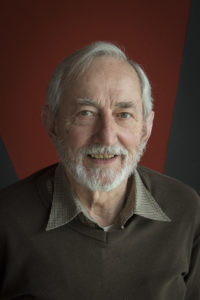
Jim Duncan passed away in 2012, but John Duncan, now 86 and living in New Zealand, has seen FormFlow realised. He’s following his protégés’ progress with enthusiasm – and a suggestion or two.
Claire Whiteley
Staff writer