Researchers at the Institute for Frontier Materials have achieved a world-first in successfully 3D printing a Boron Nitride Nanotube/Titanium composite.
The breakthrough has significant implications for industries such as aerospace, defence, automotive, energy and health.
“Boron Nitride Nanotubes (BNNTs) are an advanced new nanomaterial with many unique properties. They are ultralight, super strong and incredibly resistant to heat,” said Alfred Deakin Professor Ying (Ian) Chen, Chair in Nanotechnology at Deakin University.
“However, in the 20 years since the material’s discovery, it has only been possible to produce in small amounts. This has seriously limited its practical use in product development.
“Our novel and scalable manufacturing process can effectively eliminate this production bottleneck and unleash the real power of BNNTs into the marketplace.”
The successful demonstration of BNNT 3D printing is the result of an Institute for Frontier Materials (IFM) collaboration between Prof Chen’s nanotechnology team and the additive manufacturing team, led by Dr Daniel Fabijanic.
Prof Chen explained that the unique qualities of BNNTs mean the ability to produce larger quantities will revolutionise the material’s use in multiple industries.
While BNNTs have a structure similar to carbon nanotubes and share the same extraordinary mechanical properties and thermal conductivity, they are able to withstand double the temperatures (up to 800° C).
This superior heat tolerance is critical for surviving the extreme temperatures involved in melting and liquefying powders during the 3D printing process for metal matrix composites.
BNNTs also have greater chemical stability and electrical insulation properties, the ability to shield against neutron and ultraviolet radiation and to generate electrical current when subjected to mechanical stress.
Unlike carbon nanotubes, they can be fashioned into transparent materials like windscreens, or dyed different colours.
[testimonial_text]When integrated into composite materials and systems, BNNTs enable entirely new classes of material performance across many industrial applications[/testimonial_text]
[testimonial_picture name=”Professor Ying (Ian) Chen” details=”Alfred Deakin Professor “]
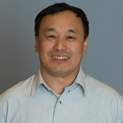
Potential applications could include metallic, polymer and ceramic composites and transparent materials for the defence and the automotive sector; thermally conductive and electrically insulating material for the semiconductor industry and sensors and structural or multifunctional applications for the aerospace and energy sectors.
BNNTs also have potential for use in batteries, supercapacitors and hydrogen storage devices for energy storage, fire retardant construction materials for the construction sector and cancer and cellular regeneration therapies.
However, the ability to realise this potential commercially has been slow until recently.
According to Prof Chen, only three organisations globally claim to be able to produce BNNTs in relatively large volume at scale.
However, the process is costly and energy intensive, which may make it difficult to sustain for large scale industrial manufacturing.
“In contrast, the Deakin BNNT technology promises to offer the highest production rate as well as being more energy efficient and industry friendly, as it is based on current industry equipment,” Prof Chen said.
“It has been demonstrated at laboratory scale at Deakin and has been running as needed to produce enough BNNTs for both internal and external research purposes, including several different products such as BN nanotube film, coatings and buckypapers, which are not available elsewhere.
“BN buckypapers could be used in aircrafts as a radiation shielding layer, as filters for removing contaminants from water, and to make lightweight and stronger vehicles and aircraft,” Prof Chen said.
Deakin has patented its BNNT production technology ready to be scaled up to meet the increasing demand for BNNTs and plans to build a commercial BNNT pilot plant at its Waurn Ponds campus to produce BNNTs in kilogram quantities.
For more information, contact Deakin’s Commercial Manager, Mr Lin Zhang or Senior Commercial Manager – Defence Technology, Mr Matt Jones
- IFM’s nanotechnology research is a part of the Deakin’s display at the Australian International Airshow and Aerospace and Defence Exposition this week, along with research from the Institute for Intelligent Systems Research and Innovation, the Faculty of Science, Engineering and Built Environment, the Deakin Software and Technology Innovation Laboratory, and industry partners demonstrating the University’s expertise in aerospace and related fields.
This article was published by Deakin Research on 1 March 2017.