The Australia-India Strategic Research Fund has announced it will support a major collaboration into high performance alloys.
A team of Deakin researchers will lead the Australian arm of a collaborative research project that aims to achieve improved performance and cost savings through advanced manufacturing of new high entropy alloys.
The research is expected to result in step changes in component performance, resulting in significant energy and cost efficiencies across three critical sectors: energy, aerospace and mining.
The Australia-India Strategic Research Fund (AISRF) announced the grant, valued at almost $1 million, as one of seven successful projects, on April 11.
[testimonial_text]This is a fantastic achievement that builds on the strategic groundwork of several Deakin researchers in India over the past 15 years[/testimonial_text]
[testimonial_picture name=”Professor Peter Hodgson” details=”Deputy Vice-Chancellor (Research) – Chief Investigator”]
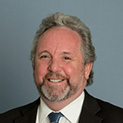
“A feature of this project is that it is multidisciplinary, involving researchers from the Institute for Frontier Materials and the Centre for Pattern Recognition and Data Analytics (PRaDA),” he added.
“It will draw on our new, sophisticated 3D metal printing equipment and a unique algorithm created by PRaDA that will allow us to fast track the development of a new class of highly important alloys.”
High entropy alloys are a new class of alloys with outstanding potential for providing enhanced durability and energy reductions. They resist creep and oxidation at high temperatures and are remarkably strong and ductile. They wear and corrode very slowly. With such a promising array of properties, there are significant efficiencies to be realised.
The challenge to be addressed by the research team concerns manufacturing. While obtaining uniform properties and accurate component shape using conventional methods has been formidable, the researchers will seek to pioneer new high entropy alloy components and compositions via advanced powder-based processes, additive manufacturing (3D metal printing) and spark plasma sintering (or pulsed electric current sintering).
The project will build on existing relationships between Deakin and the Indian Institute of Technology Madras (Indian project leader), the Indian Institute of Science Bangalore and General Electric (Bangalore), as well as with researchers at Monash and RMIT.
It will also exploit Australian ties into the commercial sector through the new Deakin-based ARC Industry Transformation Training Centre in Alloy Innovation for Mining Efficiency (mineAlloy), and the ARC Industry Transformation Research Hub in Additive Manufacturing, based at Monash.
“Through these relationships, we will have a clear path to take-up of scientific outcomes,” said Australian project leader, mineAlloy Director Professor Matthew Barnett.
“In Australia alone, the wear of components in the mining industry costs about $900 million per annum in replacement and machine down-time. We aim to double the wear life relative to current benchmark alloys.
“This project will position India and Australia to be more active in the high performance alloy market, estimated at USD 7.51 billion globally in 2015, with an approximately seven per cent growth trend, year-on-year.”
Other Deakin Chief Investigators are senior mineAlloy researcher Dr Daniel Fabijanic and Director of PRaDA, Professor Svetha Venkatesh.
“In the aerospace and energy generation sectors there is a continual demand for hotter operation for improved engine/generator efficiencies,” added Professor Barnett.
“These efficiencies equate to lower energy costs for consumers. Also, reduced fuel consumption has clear environmental and economic benefits for the civilian air transport industry. Material development needs to keep pace with operational demand.”