An academic / industry collaboration has created an approach likely to lead to a ‘step change’ in developing new materials, with huge potential to boost innovation.
A team of world-class experts at Deakin University and their enterprising industry partner have developed an entirely new way to optimise processes for manufacturing new materials, from short fibres, to alloys, to cosmetics, to food, or, in fact, any material for industry or consumer use.
By using machine learning and Bayesian mathematics (a sophisticated form of probability), the group has developed an abstract framework and software that achieves a faster, cheaper and more effective approach to optimising products and manufacturing processes.
Commercial ventures within the Geelong Future Economy Precinct on the Waurn Ponds campus are pioneering the use of the ground-breaking methodology.
A number of researchers from Deakin’s Centre for Pattern Recognition and Data Analytics (PRaDA) and Institute for Frontier Materials (IFM) were involved. The PRaDA team was led by Dr Sunil Gupta and Dr Santu Rana and the IFM team was led by Dr Alessandra Sutti.
“This breakthrough offers a very powerful tool with huge potential for many industries,” said project leader and world-leading IT expert ARC Laureate Fellow Professor Svetha Venkatesh, Director of PRADA.
[testimonial_text]We were able to develop this new method, which we call Adaptive Experimental Optimisation, through an alignment of world-class experts in machine learning, mathematics, physics, chemistry, materials, world-class facilities at Deakin and an innovative industry partner, HeiQ Australia.[/testimonial_text]
[testimonial_picture name=”Professor Svetha Venkatesh” details=”Director of PRADA”]
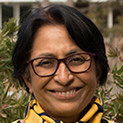
The breakthrough was recently published in the prestigious “Scientific Reports.”
“The collaboration was inspired by the challenges of industrial innovation,” said Dr Murray Height, CEO, HeiQ Australia. “We needed to efficiently generate knowledge about a novel technology with very tight timeframes, to bring a product to market.
[testimonial_text]Adaptive Experimental Optimisation has given us a fast and powerful way to accelerate product development and implement advanced manufacturing processes.[/testimonial_text]
[testimonial_picture name=”Dr Murray Height” details=”CEO HeiQ Australia”]

“When businesses go about developing a new product or process, there is often enormous complexity in the range of variables they face, which can become expensive and unwieldy when running experiments, both in the lab or as large-scale trials on the factory floor.
“With this approach, we can rapidly optimise our products and processes. This methodology has clear potential to benefit material and process-oriented industries seeking efficient and nimble innovation.”
“Adaptive Experimental Optimisation allows us to be a hundred to a thousand times faster than conventional ‘design of experiment’ methods,” added IFM researcher Dr Alessandra Sutti.
“It is an immense task to optimise not just the novel materials we make, but also the new, little-characterised, manufacturing processes associated with them.”
[testimonial_text]In terms of real savings: instead of 100-150 experiments using traditional methodologies, we optimised the short fibre processes and products in 10. This is a step change in the way people talk and think about experiments.[/testimonial_text]
[testimonial_picture name=”Dr Alessandra Sutti” details=”IFM Researcher”]

The team assists HeiQ Australia to develop world-first short fibre materials that offer enormous potential in textile applications. Its first product, HeiQ Real Silk, reproduces the luxurious tactile properties of silk and the short fibre material is manufactured in the Geelong Innovation Precinct at Waurn Ponds. This export product is used in the global textile market, including in apparel and home textiles, such as bedding.
The PRaDA research team used the same methodology in the RAPID joint venture being set up at Deakin in collaboration with researchers from IFM. Rapid Alloy Process, Innovation and Design (RAPID) uses cutting-edge software to reduce production time and costs in alloy manufacturing, while improving properties such as weight and strength.
“With new materials and new processes – unlike an established material like steel, for instance – the legacy knowledge base is often limited. The computational models don’t exist and the cost of building new ones is very high,” explained Professor Venkatesh.
“We don’t have a complete data set for new materials, so we have to generate knowledge through experimentation. Machine learning allows us to be nimble, so we can optimise new materials using a handful of experimental data points – or lean data. The software acts as an experimental assistant to help navigate experimental complexity.”
“Rapid Bayesian optimisation for synthesis of short polymer fibre materials,” “Scientific Reports.”
Contact Ben Spincer, Director, Deakin Research Commercial, for more information.
Main photograph: (from left) Dr Sunil Gupta, Dr Alessandra Sutti, Professor Svetha Venkatesh and Dr Murray Height.
Published by Deakin Research on 30 August 2017